RESEARCH PHILOSOPHY AND
TRANSLATION
We are one of the UKs leading academic groups in the bottom up synthesis, discovery, optimisation and scale-up of advanced functional inorganic materials. We make materials from the outset with scale up in mind, therefore we are able to go from low technology readiness levels (TRLs) to pilot scale demonstration of materials and devices. We have a number of synthesis processes and facilties as well as analytical facilities within the group which are avilable for our researchers and associated masters and other students. In order to maintain safety and good practice, we run a quality system for the training and use of all our facilties.
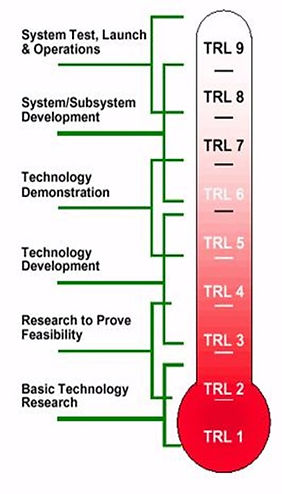
HOW DO WE DESIGN OUR EXPERIMENTS?
We generally work towards either a target material or within composition space of several metals where we are seeking to optimise a specific property or performance, e.g. gravimentric capacity for Li-ion cathode. Typically, we will create a design of experiments approach in which a libray of samples is generated and then screened. The data from this can then be fed back into the synthesis in order to rapidly optimise performance.
ACCELERATING MATERIALS DISCOVERY TO SCALE UP

STEP 1: PRECIPITATION
1) If the materials can be made directly using our suite of hydrothermal reactors, and or is required to be nano-sized, we would favour using one of the suite of Continuous Hydrothermal Flow Synthesis (CHFS) reactors that go from lab to pilot scale (images below). A review of materials that can be made in CHFS can be found here via this LINK. Alternatively, libiraries can be made using room temperature flow reactors (incorporating dynamic mixing) known as the ACTIM process, which is more industry relevant as it offers a lower CO2 footprint in terms of energy comsumption. The key thing is to ensure that all metal ions are well mixed in the obtained precipitate.

Figure 1: CHFS process schematic on top left, patented confined jet mixer of CHFS (middle) and pilot plant CHFS photo (right). To see a review on CHFS, see Chemical Reviews 2017, 117, 11125 or see LINK.
STEP 2: CLEAN SAMPLES / ADD REAGENT?
3) All samples made in STEP1 must be cleaned of residual ions and then dried prior to use or prior to a further heat treatment. In the special case where a reagent needs to be added after STEP1, e.g. Li or Na, then this is added with good mixing and careful drying to ensure that the added ions are homogenously mixed.

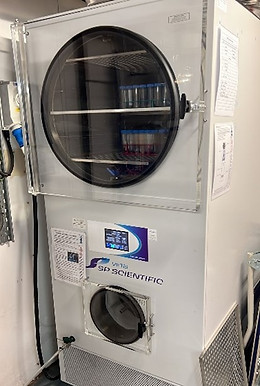

Figure 2: Mixers for Li source additions (left), large scale freeze dryer (middle), unlithatated precipitate powder prior to Li source addition and flash heating.
STEP 3: LAB SCALE HEAT-TREATMENT OF MATERIALS LIBRARIES
If the materials libraries from STEP1 or STEP2 need to be heat treated, we can heat treat samples in FLASH static tube furnaces from a few seconds to a few hours. Typically, in FLASH heating the samples are added to a pre-heated tube or box furnace for a few minutes and then are quench cooled in air to lock in specific defect states or phase mixtures. Samples from STEP3 can then be screened via XRD or other methods such as in coin cells if they are battery electrode materials.

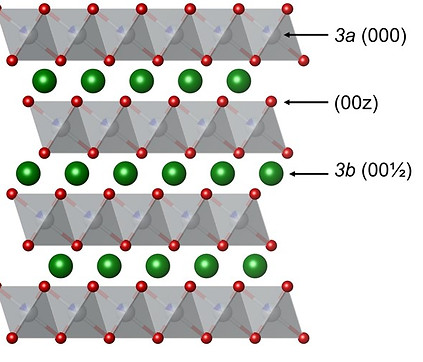

Figure 3: typical library of materials made via CHFS or AMTIM process, in this case, showing a range of compositions (left) and diagram of the layers in a typical layered cathode Li-ion battery material in which defects can be tuned to give optimal properties (middle) and coin cells for high throughput testing of battery active materials (right).
STEP 4: SCALE-UP OF LEAD MATERIALS TO KG-SCALE
Then the synthesis of lead materials can scaled up using a range of UCL's furnaces including continuous furnaces or larger FLASH furnaces, that offer a range of heat treatment conditions which can be matched to the small scale heat treatment. Such lead materials can again be analysed or tested in larger demonstrators (e.g. battery pouch cells) to ensure they have similar performance to the lead materials at the small scale.
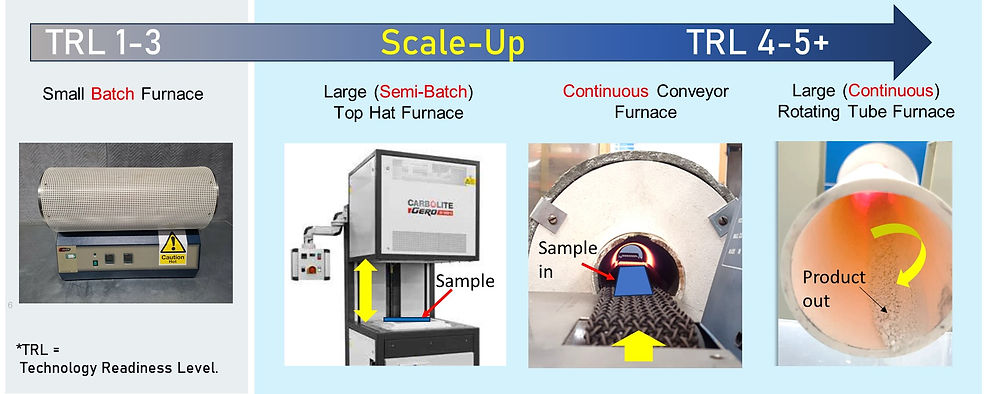
Figure 4: Static FLASH furance (left), followed by TOP HAT furance, Conveyor furnace and on the far right, rotating tube furnace.
STEP 5: DEMONSTRATOR DEVICES
If the materials libraries have been scaled up, sometimes in mutiple Kg level, we can thus assemble larger scale demonstrator devices to show progression up the Technology Readiness Levels (TRLs). In the case for battery materials, this would be in the form of a large scale single or muti level pouch cell for example.

Figure 5: multilayer pouch cell made using large scale materials production